Examples of applications surface grinding and polishing

3D component processing
Our bottle opener processed
3D component processing
This is what our bottle opener should look like when it is 3D printed.

3D component processing
We have selected our high-speed centrifugal systems for processing this bottle opener.
Polishing brass instruments
After processing
Polishing brass instruments
Before processing
How can the mirror finish be achieved?
Processed with walnut granulate and various compounds. To achieve a mirror finish on the surface, several polishing cycles in a high-speed centrifugal system are necessary. It can be between 3 and 5 cycles, depending on the desired result and surface condition before processing.

Titanium part
Component after processing

Titanium part
Task: Removing milling stripes and polising

Processing titanium parts
We processed the titanium component in 2 cycles of 60 minutes each. First the component was grinded from milling stripes. The polishing was then carried out in the 2nd cycle. The processing took place in one of our high speed centrifugal systems, a combination of wet and dry processes.

Satinizing
Component after processing

Satinizing
Task: a matt gloss should be created

Satinizing
The processing was carried out in the dry process in a round vibration system, using special media in nugget form. The peculiarity of these media lies in the fact that the surface is matt and has a beautiful shine, satin.

Acrylic component: satin finishing
Before / after view

Acrylic component: satin finishing
Before / after view

Acrylic component: satin finishing
The acrylic components were processed with our special nuggets for satinizing surfaces. Processing is possible in all common grinding systems. It is a dry process.

3D component: titanium
Titanium component grinded and polished

3D component: titanium
Titanium component after it was created by 3D printing

3D component: titanium
The result after 2 cycles in our high-speed centrifugal systems.

Deburring O- rings with a thickness of 2mm
Grinded and deburred

Deburring O-rings with a thickness of 2mm
Burrs are clearly visible

Deburring O- rings with a thickness of 2mm
Depending on the thickness of the material, alloy and size of the component, different grinding medias were used, differing in shape and composition.
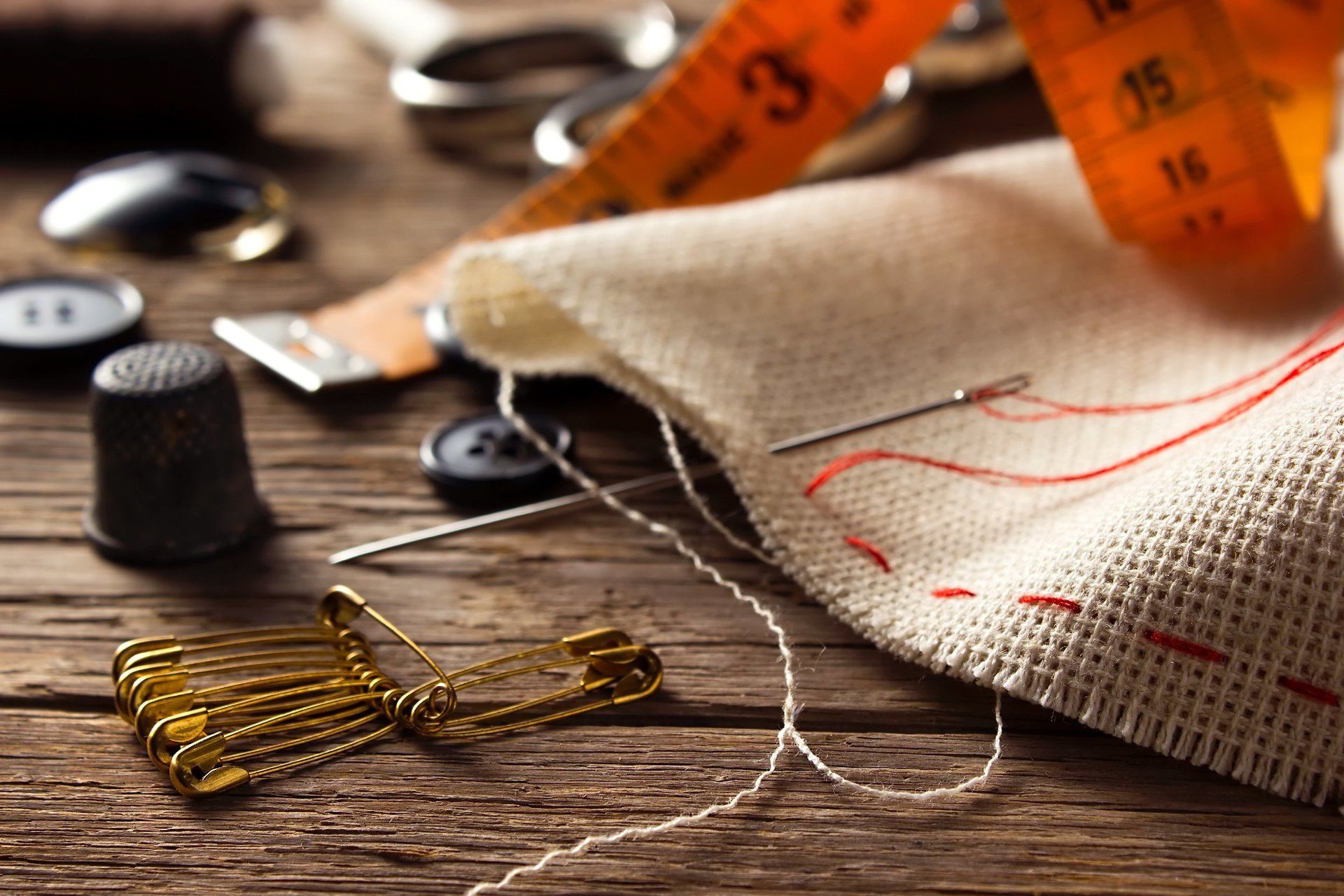
Textile machine industry
Spare parts for textile machines can be successfully processed, even very narrow and angled areas can be processed and the surface can be rounded and smoothed.
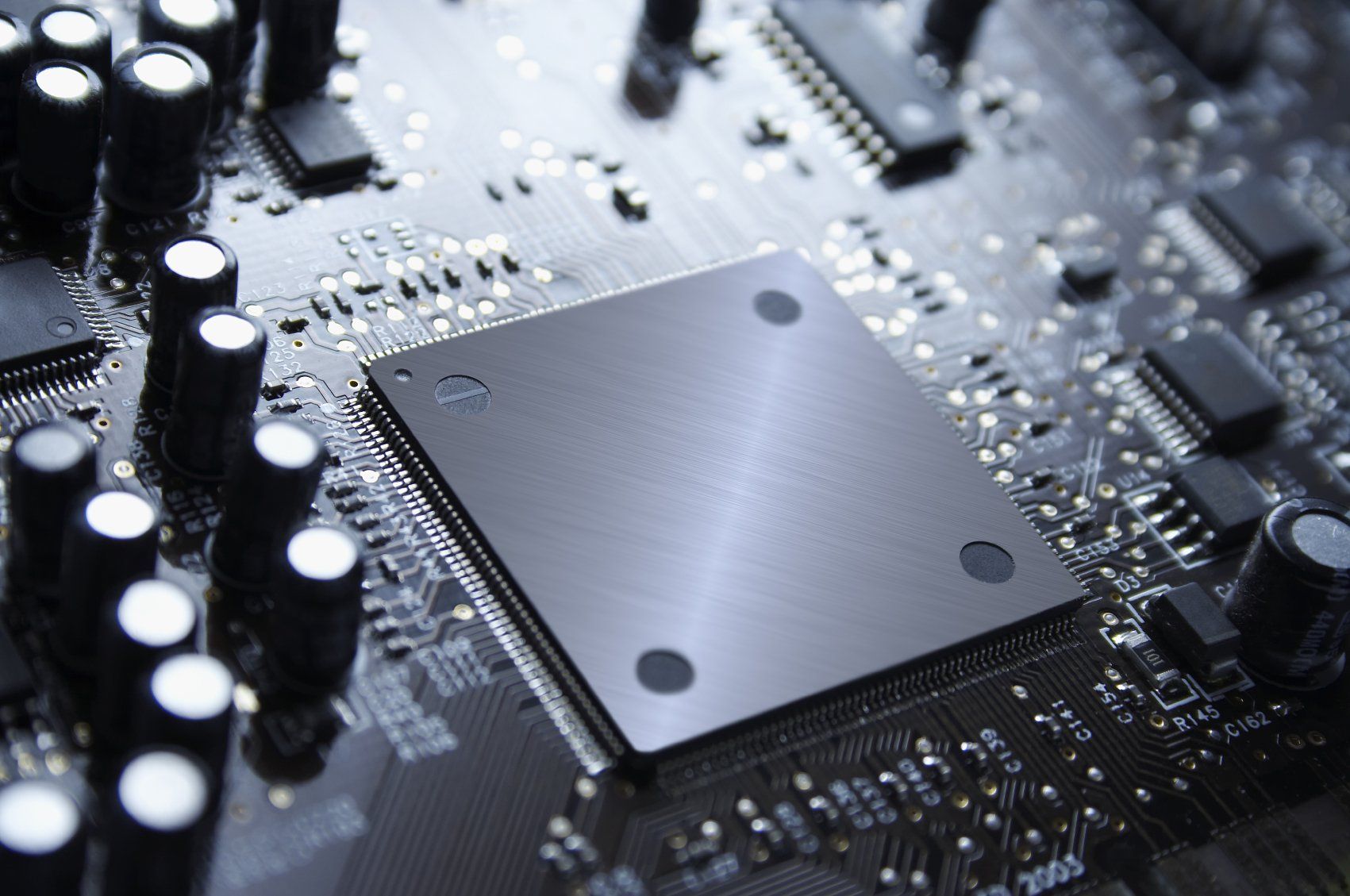
Electronics: deburring copper component
The deburring of copper components is possible using ceramic grinding medias and our high-speed centrifugal systems. Cycle times between 13 and 30 minutes.
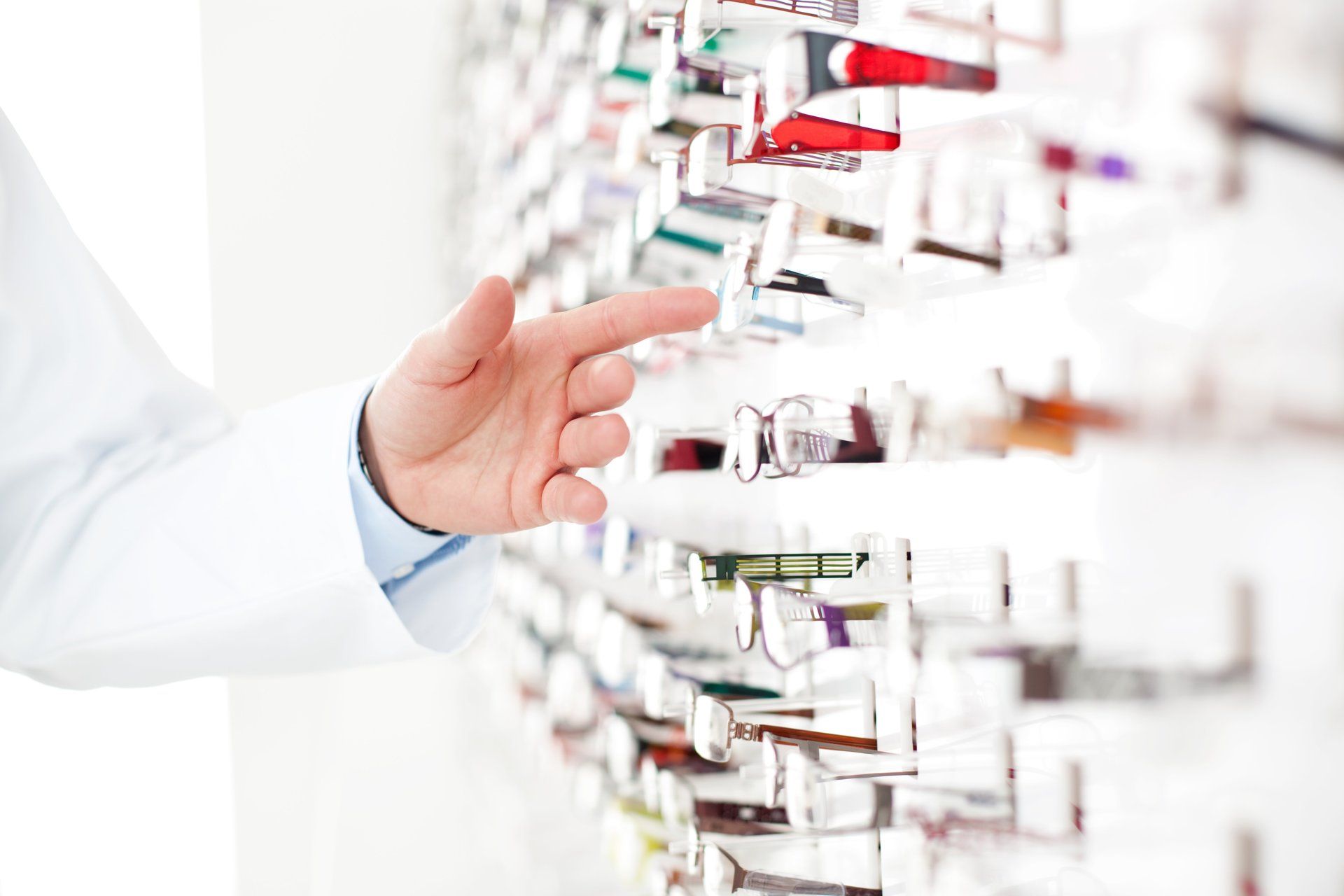
Polish very high-quality temple pieces
As with brass instruments, high-quality designer eyeglass temples can be finely grinded and polished to a mirror finish in 2-3 cycles.
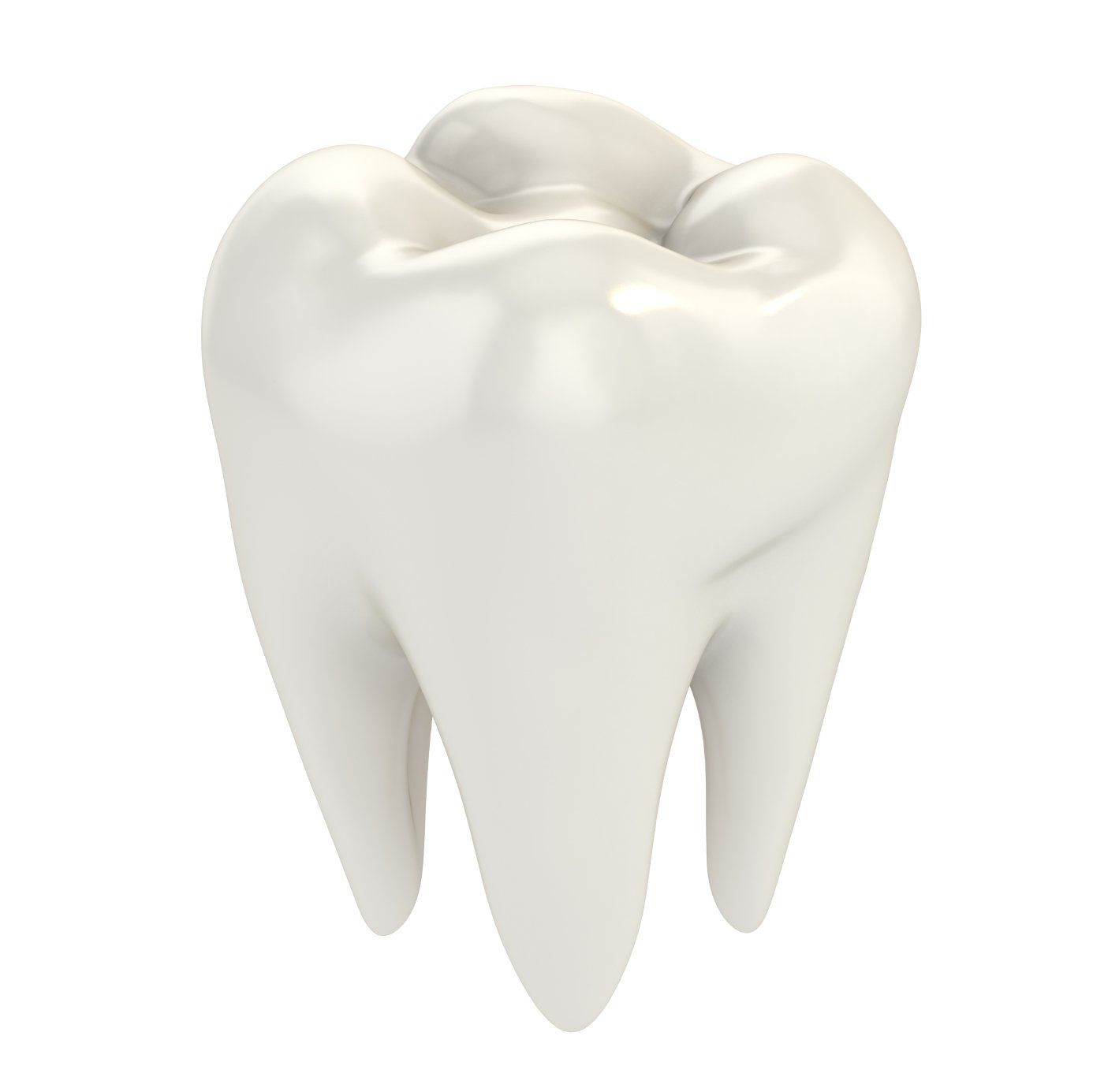
Medical technology: dental implants / knee implants / hip implants
Free from milling stripes, 3D printed components, grinding and high-gloss polishing, components of different sizes, properties and shapes are possible to process.
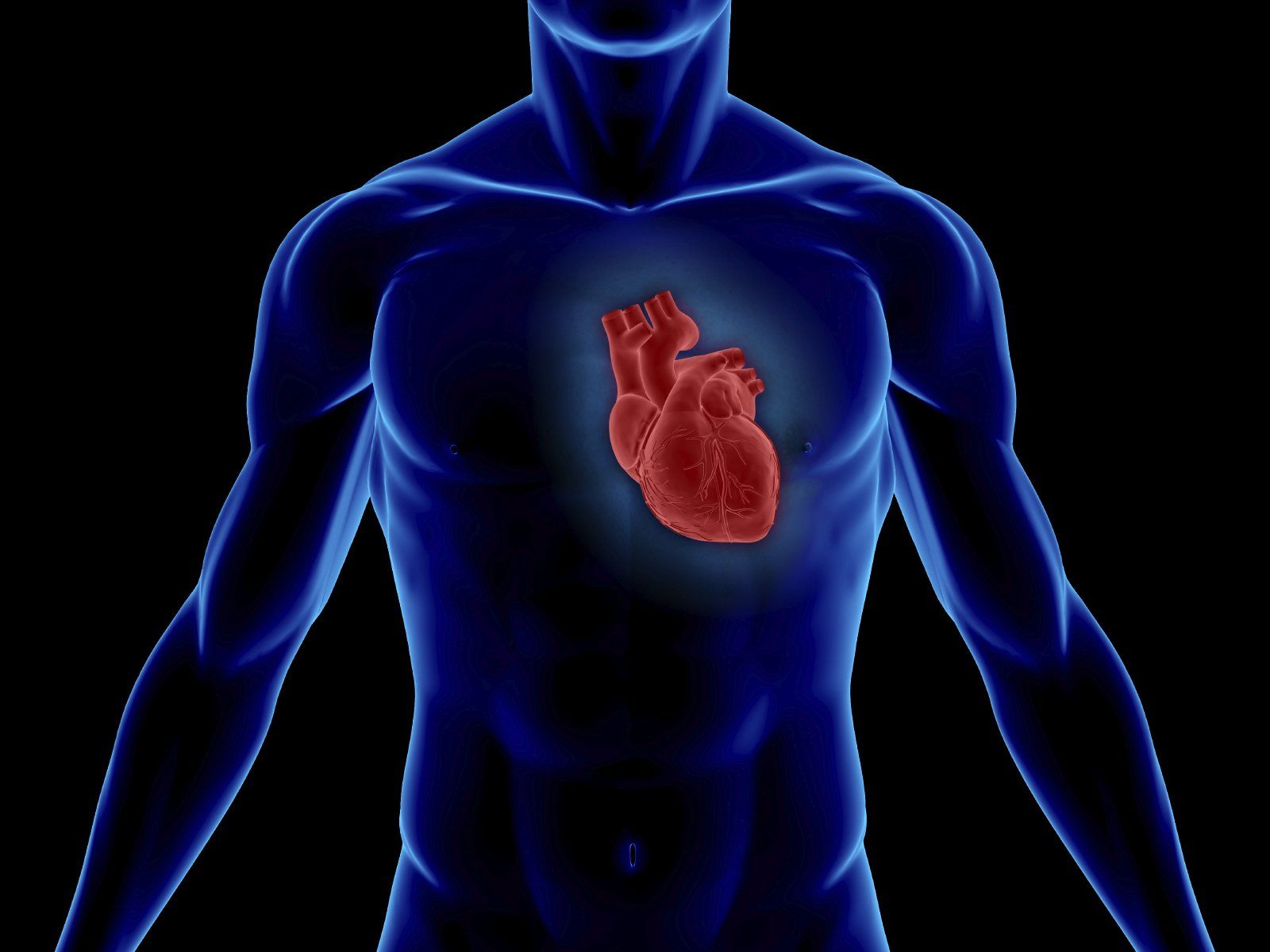
Medical technology: components from highly sensitive areas
Our high-speed centrifugal systems and our specially manufactured grinding medias are also suitable for these applications. Medias and systems have been specially coordinated for this application.
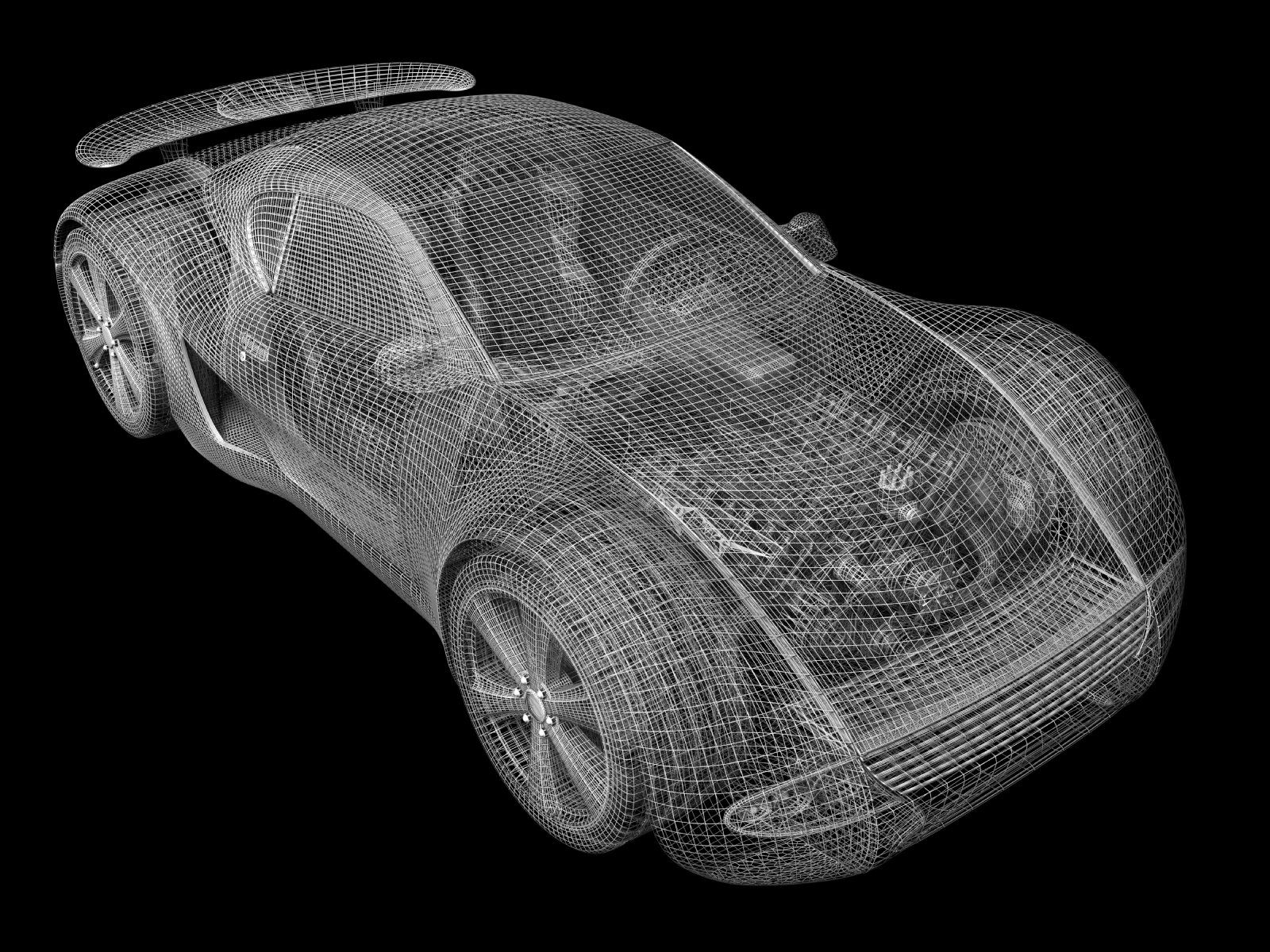
Automotive
Our media and systems are used in various automotive fields. It is possible to machine small components, too.
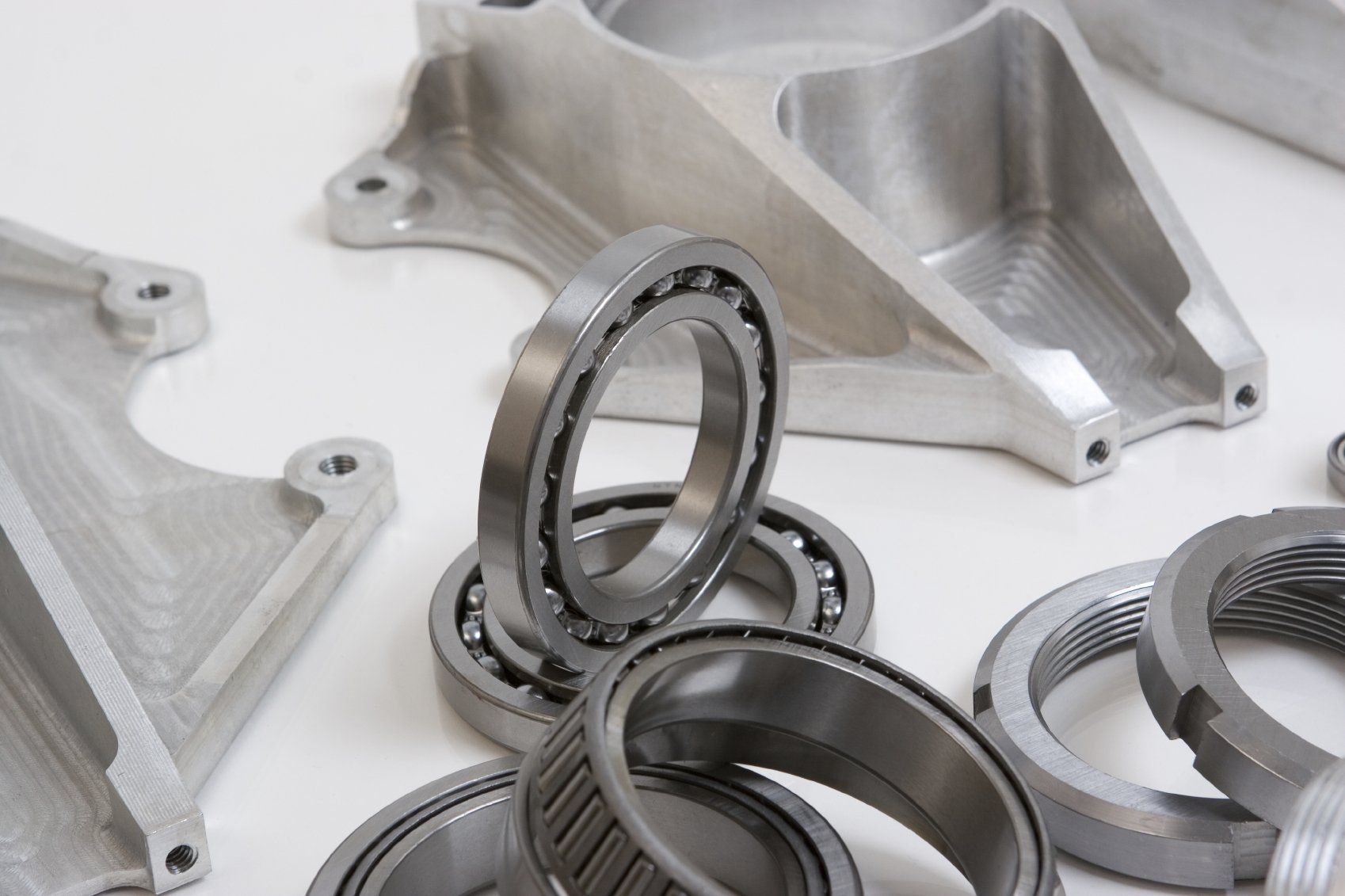
Rolling bearings / ball bearings / valves
Low surface roughness can be achieved, less than 0.3µm.
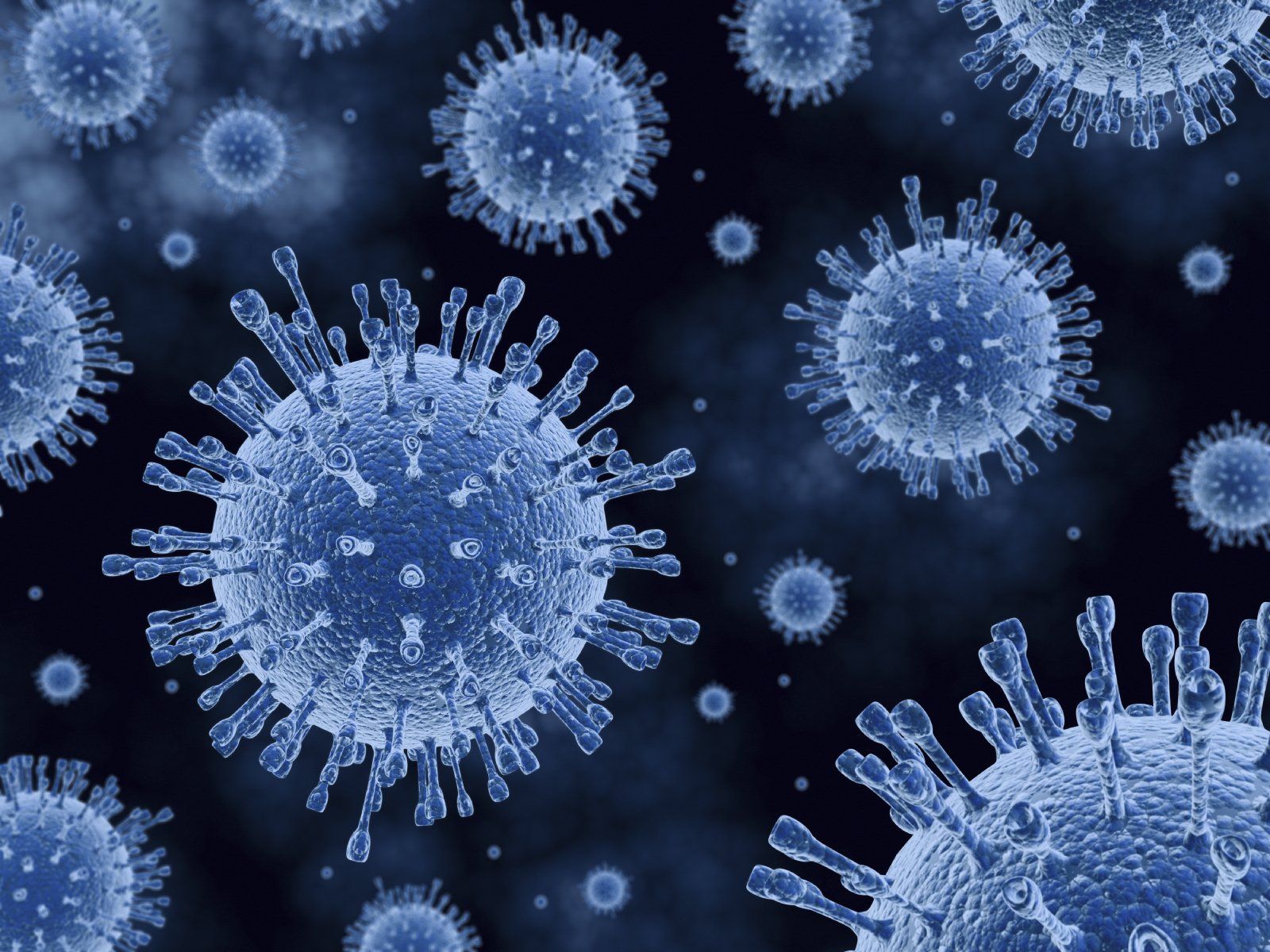
Polish components with zinc coating
Used in medical technology, components with a very thin zinc coating to ward off bacteria can be polished.
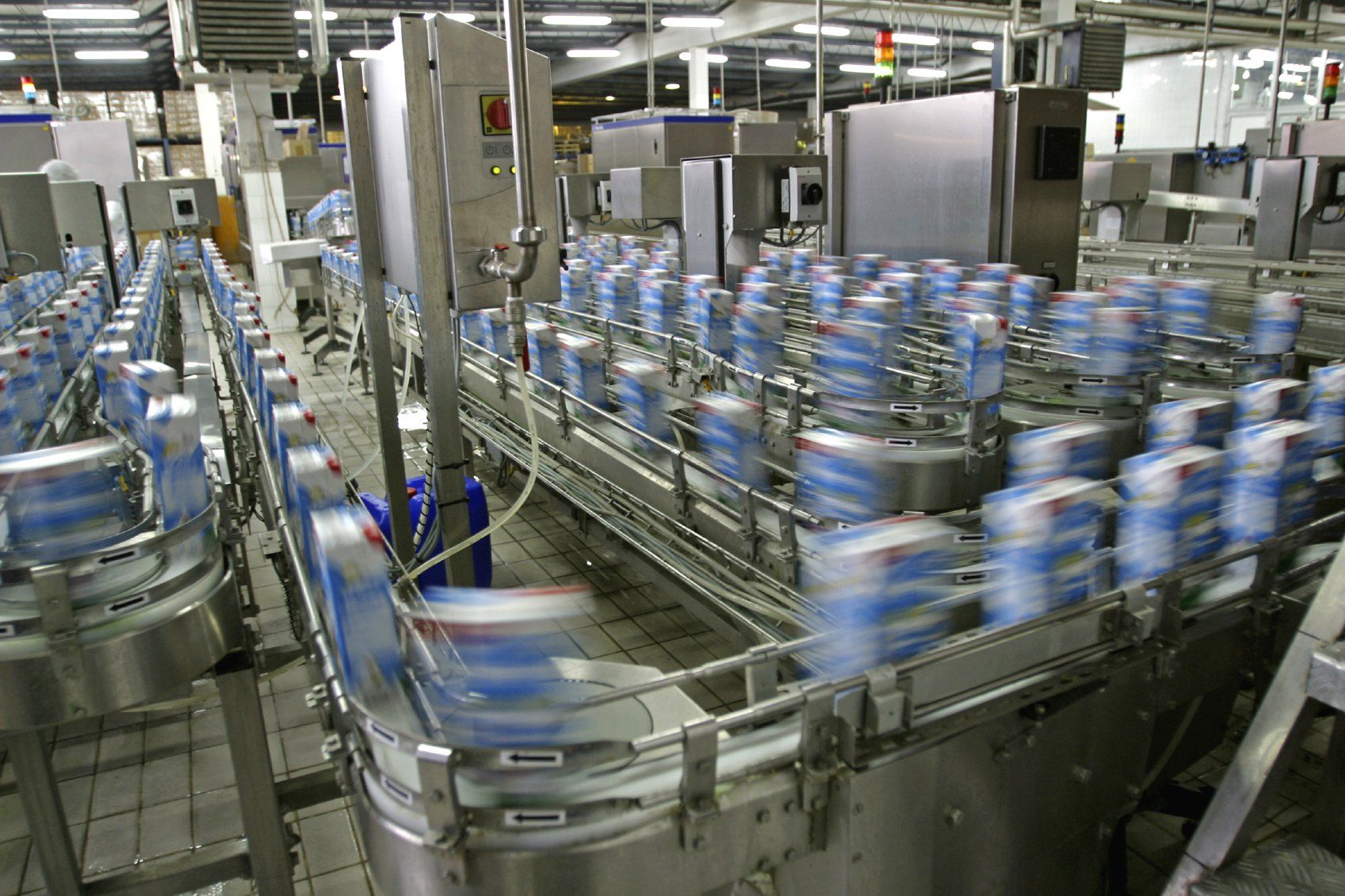
food industry
Our grinding medias are also used in this area. Highly abrasive, they create a homogeneous, smooth surface. Large and small components can be removed from milling spripes and prepared for electroplating.









